Can tech-challenged countries leapfrog to 3D printing?
Undoubtedly, manufacturing is the old guard of the economy. For a country, it is either you manufacture or you perish; meaning your economy will suffer and you will forever be vulnerable as you depend on others to meet your basic needs. While countries like the United States and many in Europe possess a spectrum of […]
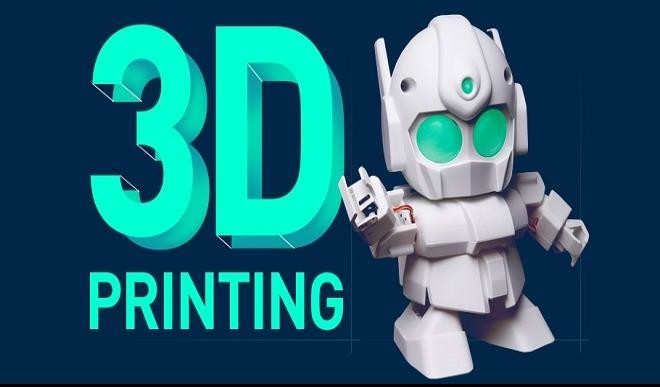
Undoubtedly, manufacturing is the old guard of the economy. For a country, it is either you manufacture or you perish; meaning your economy will suffer and you will forever be vulnerable as you depend on others to meet your basic needs. While countries like the United States and many in Europe possess a spectrum of knowhow that inched them into the arena of civilization, Asian countries – exemplified by Japan and South Korea – have earned the title of being developed based mostly on their country’s manufacturing prowess. Even China, the notoriety it has acquired in the past decade has been rooted in the country’s strategic focus on manufacturing. So, manufacturing is serious matter.
As pointed out in a previous article in this column, the most distinctive feature of 3D Printing is that it is an additive manufacturing process. This is unlike injection or compression moulding of plastics or the casting of metals. In these processes, you fill a cavity in the shape of the build material with the flowing form of the material, followed by cooling and solidification. In subtractive manufacturing, which is a common traditional manufacturing process, you start out with a block of the build material, and systematically remove (subtract) parts in order to arrive at the desired shape of your object. On the other hand, 3D Printing builds parts up additively, layer by layer, using a variety of ways that depend on the particular process used. Furthermore, traditional production systems often require expensive tooling, fixtures, and the need to assemble parts. Subtractive processes lead to significant waste of materials.
3D printing, which was conceived in the early eighties, started out as a prototyping method; or, more specifically, as a Rapid prototyping method. This involves rapidly producing – often geometrically-scaled down replicas (prototypes) of an object (in a rapid fashion) that allows you to carry out many iterations until the process is perfected and the actual object can be built.
Additive manufacturing (AM), which, as alluded to above, refers to the common technique used in 3D printing wherein the parts are successively (additively) layered, started with the manufacturing of complex plastic parts, but it has now been extended to the fabrication of intricate metal parts. The attractiveness of AM includes the automation, with the specific advantage that you do not need to have any real skills in manufacturing processes before you build your parts. The technique is quite amenable to high speed fabrication and the ability to fabricate complex parts. It requires that computer-aided drawing of the part, generated using computer-aided design (CAD) tools such as AutoCAD, NX, and Pro-Engineer, be fed into computer-controlled fabrication machines, which automatically fabricate the physical component using the information contained in the digital file.
So far-along is 3D printing that the United States Navy is 3D-printing submersible vehicles. Andrew Liptak describes this in his 29 July 2017 article, saying that: “Militaries around the world have eyed 3D printing as a cost and time-effective resource for future missions, whether it’s printing up replacement parts for warplanes, grenade launchers, or meals for soldiers.”
The Navy team that is building up the sea vehicles reportedly began their work in August 2016, using a “massive industrial 3D Printer called Big Area Additive Manufacturing (BAAM) to manufacture six carbon fibre sections, which were then assembled into the 30 foot long vehicle.” According to Liptak, the team was given four weeks to develop the hull, spending the first week designing it, and began printing the components a week later. It’s now the Navy’s largest 3D printed asset. Liptak, quoting the US Department of Energy, says that a traditional hull “ranges from $600,000 to $800,000 and typically takes 3-5 months to manufacture,” while this 3D-printed version was 90 percent cheaper and was produced within “a matter of days.” The value of fast turnaround cannot be underestimated, especially in military matters. Note, however, that the fabricated vehicle alluded to in this article is not a working machine, but rather a proof-of-concept; but the team is reportedly on its way to printing up a second, watertight version of the submarine that will undergo practical water testing, with “fleet-capable prototypes” that could potentially be introduced for use as early as 2019.
Obviously, poor and emerging countries wouldn’t be focusing on the 3D printing of military arsenals, but will be expected to rather focus on more existential objectives. Moreover, the tech-challenged countries of the world have not mastered the more traditional manufacturing processes. The question then is whether or not they can just leapfrog to advanced manufacturing using AM, without making up for the deep slack in the traditional, high-skill-demanding manufacturing processes. It seems this is a possibility, particularly if the AM technique is developed to perfection, rendering the manufacturing of virtually any mechanical part a “black box” operation. Poor and emerging countries have leapfrogged before; for example, on telephony and smart devices. That is, virtually everyone in most African countries has a cell phone today; whereas the technology of landline telephony in those countries is far from being well developed.