How absence of long fibre pulp crippled Nigeria’s paper industry
…Expert proffers solution The absence of long fibre pulp has been identified as one of the major factors that incapacitated Nigeria’s efforts to be self-sufficient in paper production. Experts believe it has led to the closure of the country’s foremost paper mills, forcing us to mostly depend on importation of writing, printing and newsprint […]
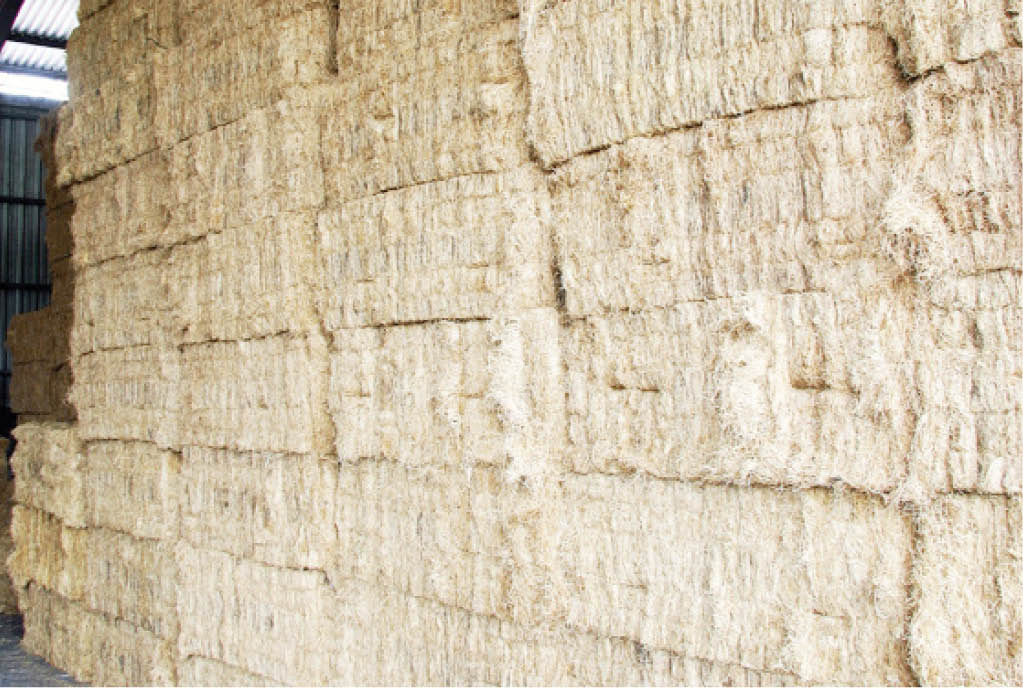
Palm dried long fibre
…Expert proffers solution
The absence of long fibre pulp has been identified as one of the major factors that incapacitated Nigeria’s efforts to be self-sufficient in paper production. Experts believe it has led to the closure of the country’s foremost paper mills, forcing us to mostly depend on importation of writing, printing and newsprint papers.
The pulp and paper industry in Nigeria was one of the major industries that performed well in the 1970s and 1980s, before the oil glut era.
Self-sufficiency in paper production was one of the major cardinal objectives of the government in the 1960s and 1970s. This was evidenced by the establishment of three integrated pulp and paper mills between 1969 and 1976. Two of the mills – the Nigeria Paper Mill, Jebba and the Nigeria Newsprint Manufacturing Company, Oku Iboku – performed optimally and paper importation faded out in the 1980s.
According to a document from the Raw Material Research and Development Council seen by Daily Trust on Sunday, Nigerian paper mill’s actual production in 1985 was 40,480mt, and in 1986, 42,960 tonnes, representing 62.3 per cent and 66.17 per cent capacity utilisation respectively. This pattern of capacity utilisation was also experienced in the Nigerian Newsprint Manufacturing Company (NNMC), Oku-Iboku, about the same period.
According to the document, the volume of production at the NNMC rose from 28,927 tonnes in 1989 to 37,581 tonnes in 1990.
Due to the establishment of the NNMC, importation of newsprint reduced drastically to 17.5per cent in 1986 and 12.5per cent in 1987 respectively and faded out in 1988.
However, due to the downturn in the economy in the 1990s, the integrated mills convulsed and capacity utilisation nosedived.
The document shows that capacity utilisation at the Nigeria Paper Mill went down as low as 2.5per cent in the early 1990s until the mill stopped production in 1996. The third pulp and paper mill, the Iwopin Pulp and Paper Company, were established in 1976 to produce fine writing, printing and cultural papers. By 1983, when the mill was at 85per cent completion, it was abandoned, and up till the time it was shut down in 1998, the mill did not produce up to 5per cent of its installed capacity.
In line with the privatisation agenda of the Federal Government, the primary pulp and paper mills were privatised in 2006. Although the Nigeria Paper Mill, Jebba, has commenced production of kraft paper on one of its paper machines, the two other mills are yet to commence production. This situation has seriously affected the pulp and paper industry in the country; and today, we mostly depend on importation of writing, printing and newsprint papers.
Challenges of optimal pulp and paper production in Nigeria
Experts believe a number of problems are militating against optimal pulp and paper production in Nigeria.
The director-general of the Raw Material Research and Development Council Professor, Hussaini Doko Ibrahim, noted that one of the major challenges was that the integrated pulp and paper mills in Nigeria depended overwhelmingly on imported long fibre pulp. According to him, the forests in Nigeria consist predominantly of mixed tropical hardwood species which fibre lengths vary from 0.8mm to 1.6mm. He said that fibre length was an important factor influencing strength development in the paper industry.
“As the integrated pulp and paper mills established locally are expected to produce fine writing and printing papers, kraft paper and newsprint, the mills require long fibre pulp to mix with the short fibre pulp to enable development of strength required by each of the products,’’ he said.
Ibrahim observed that one of the major problems of the mills is the high cost of importing approximately 85,000 tonnes of long fibre pulp required in the process. As at 1990, he said approximately $85 million was required to import 85,000 tonnes of long fibre pulp and about $20 million required to import different types of chemicals required by the mills.
“The oil glut of the era made the sourcing of the foreign exchange impossible, leading to the abandonment of the mills. Today, about N500 billion is expended annually to import pulp and paper products,’’ he added.
He further said another major issue was the funding of research and development in pulp and paper science. “While the development of pulp and paper sector in the United States is fueled by adequate funding of research and development projects as it is mandatory that 1per cent of the sales of the paper and allied sectors are annually directed towards research in Nigeria, funding of forestry projects, most especially those in the pulp and paper sector, is nonexistent,’’ he noted.
The way forward for optimal paper production
Professor Ibrahim said there was a need for a deliberate strategic plan by national planners to develop the sector. According to him, one of the major areas that need a strategic approach is long fibre pulp development. He believes that kenaf bast fibre could go a long way in alleviating the problems posed by a shortage of long fibre pulp, quoting studies that indicated that the mean fibre length of locally grown kenaf is 2.90 mm while the fibre diameter was reported as 28.16um; lumen width, 6.08 um; and cell wall thickness; 11.04 um respectively.
“As a result of this, the Raw Materials Research and Development Council constituted a task force that determined the optimal parameters for the commercial-scale pulping of bastkenaf fibres in Nigeria. The report of the task force showed that bast fibre pulp of kenaf can replace imported long fibre pulp.
He, however, regretted that since the completion of the study, little or no progress had been made in securing private sector investment in kenaf long fibre pulp production as a result of the high cost of erecting a new pulp mill to use kenaf as its major raw material. He said the unwillingness of the paper mills in the country to change from the use of wood to non-wood raw material, coupled with the collapse of the pulp and paper mills in the country in the mid 1990s, had hindered the efforts.
Ibrahim said research carried out locally had shown that Sterculiasetigera and Sterculiaoblonga have long fibre characteristics. Studies have shown the fibre length to be about 2.41mm, indicating that it can be used to produce pulp with properties reminiscent of those of imported long fibre pulp. Thus the Council is working toward achieving this, he added.
Studies have also shown Sterculiaoblonga to have long fibre length. Preliminary work carried out on indigenous Sterculiaoblonga showed the average fibre length to be about 2.07mm. The strength properties of unbleached kraft paper obtained from the plant species were within acceptable range of those produced at commercial scale at the Nigeria Paper Mill, Jebba. In the light of the above, the development of the Nigeria pulp and paper industry may be premised on long fibre raw material sourcing from plantation grown sterculiaspecies.
He said bamboo should also be reconsidered for pulp and paper production. Bamboo is widely distributed in the South and Middle Belt regions of the country. Despite this, bamboo utilisation for pulp and paper production was dropped by the Nigeria Paper Mill, Jebba in the 1980s. The fibre length of Nigerian bamboos varies from 2.37-2.92mm, indicating the possibility of producing strong paper with good tearing resistance from the plant. The major problem of bamboo pulping is silica deposition as the high silica content must be taken into consideration in view of scaling problems in the cooking plant and in black liquor evaporator, which may lead to difficulty in lime pre-burning, he said.
Attracting investors to the sector
Paper production is a capital intensive activity. This notwithstanding, some people have shown interest in investing in this area, says the RMRDC boss. However, he said high dependence on imported raw materials had always been militating against this.
“This has made the need for investment promotion in the small scale mills imperative. A major advantage of small scale paper mills is the low initial capital requirement, which makes it more attractive to the small scale investor. To encourage the development of small scale pulp and paper making industries in Nigeria, the government may have to earmark certain products exclusively in the domain of the small scale paper industries and to protect them from competition from the large industries that have been privatised,’’ he suggested.
A public affairs analyst, Mr. Toyin Ajayi, suggested that it is important that tariff on products of small scale pulp and paper mills be increased and to eliminate double taxation for raw materials and products.